Hazardous Location
“Don't try this at home!”
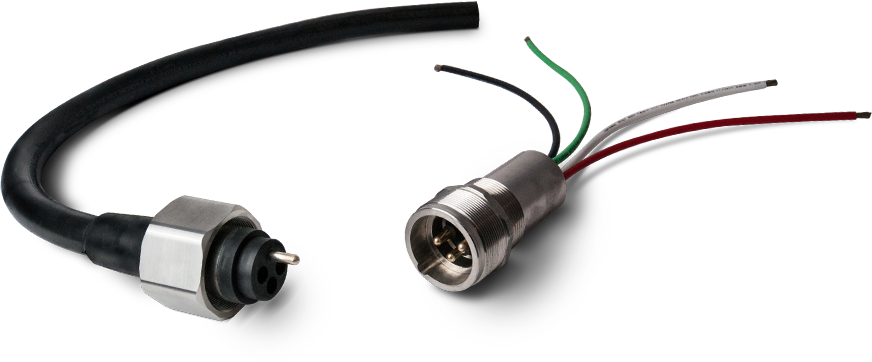
PumpSaver HL
Cable entry into a Class One Division One Group C and D Hazardous-Location pump has its share of issues depending on your perspective.
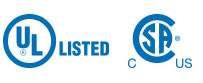
It concerns mechanical engineers because every penetration is an opportunity for effluent to get into the motor
It concerns electrical engineers because modern pumps need more monitoring, sensing and control features than ever- meaning more cables
It concerns certification managers as every jurisdiction seems to have their own requirements for cable entry
It concerns manufacturing managers because it is a slow, messy and trade-craft sensitive process that takes up a great deal of valuable floor space.
It concerns packaging and logisticians because there is no good way to protect the wired pump in transit- and if the cable gets damaged, the pump goes back for factory service
It concerns customers because their new project needs to be safe, reliable and on time
600V Service Disconnect
- Suitable for use in Pumps specified in UL 674 and 778
- Suitable for use in CSA applications in submersible pumps
- Meets the requirements for use in Class 1 Div 1 Group C and D applications
- Not suitable for disconnecting a pump under load
- High internal pressure tested- rated at 1250 Psi
- Passes extremely low-pressure seepage test (.22 Psi)
Available Configurations
Control
#18 AWG 5 Conductor- uses UL Type SOOW cable
Power
#14-10 AWG 4 Conductor- uses UL Type SOOW cable
#8-6 AWG 4 Conductor- uses UL Type W cable (up to 85A)
Features
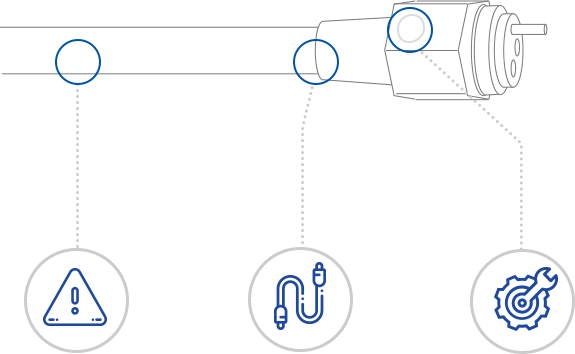
High Visibility tag says “Do Not Disconnect Under Load”
Cable to molded plug interface becomes homogenous
Coupling nut retention feature- set screw keeps the coupler thread locked in position
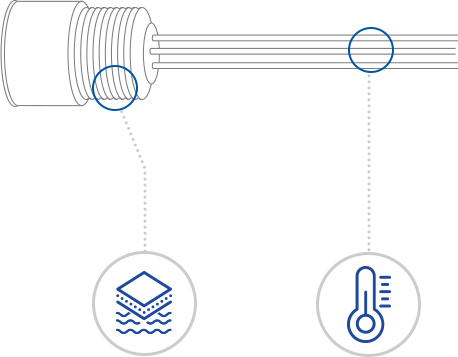
Epoxy sealing inside motor is impervious to motor-off gassing (due to hot wire insulation of varnish) of seepage from effluent
High temperature Teflon Lead wire- also chemically impervious to solvents, and offer very high temperature resistance
Construction
- Coupling nut is made from SS304 and the receptacle body is made from SS316
- Plug body is drawn from SS316
- Pins and sockets are silver-plated bronze, to maintain contact resistance
- Molding Material is Paige-developed thermoset Chloroprene elastomer
- Receptacle potting is either CSA or UL approved for use in HL and meets the requirements of pressure and solvent-resistance testing
Benefits
- Cable can be disconnected from motor, allowing it to be packaged separately for transportation or replaced in the event of damage, without costly factory rewiring of cable cap
- Cable and plug body seal to eliminate the possibility of environmental ingress up to 300m
- Cable mold can withstand tremendous stress at various angles- and will support up to 300 Lbs. of pull force without degradation
- Hydrostatic testing far exceeds UL /CSA requirements
- Plug will not vibrate loose from receptacle
- High temperature wire insulation will continue to operate in excessive current, low-water situations.
- Eliminates the need for large-footprint, low velocity in-house cable termination process- large dollar savings, and an opportunity to save space in tight manufacturing plants (cable process plus reel storage takes up tremendous amounts of space)
- Complex, smelly and messy potting process is replaced with a threaded fitting- requiring seconds to install, instead of hours
- Cost suitable in a highly competitive pump market
Coming Soon
Composite power and control constructions
Power constructions up to 240A
European Approvals